传统的解决方案是采用热处理方法消除工件残余应力,控制变形尺寸,达到稳定尺寸精度的目的。但由于这种超大型筒阀直径近10m,对热处理设备及热处理技术均有较高的要求,实施难度较大,不仅需要建造超大型窑炉,而且产生的表面氧化和热变形等问题会对后续加工产生不利影响。因此,采用振动时效技术控制筒阀的内应力。
振动时效技术是通过对工件施加动应力的方式消除残余应力,通过对多台大型筒阀进行试验验证,结果表明,振动时效对稳定大型筒阀尺寸精度有着非常显著的效果,摆脱和避免了传统热时效工艺带来的诸多限制与问题。
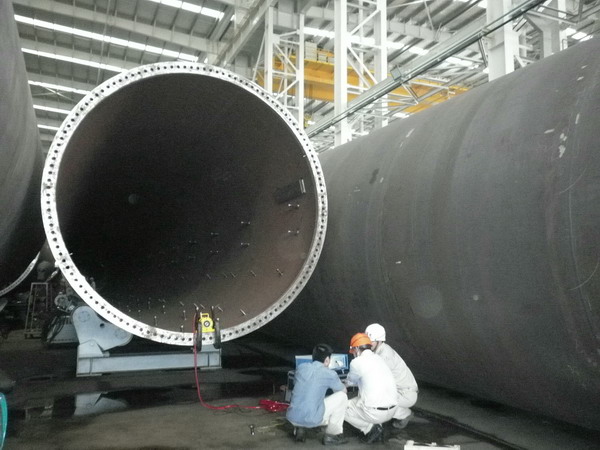
1 振动时效技术制残余应力机理
振动时效是通过激振器对工件施加周期性外力,使工件产生振动,利用振动能量来达到降低和均化残余应力的目的[2, 3]。目前,对于振动时效的机理可以从宏观和微观两个方面来理解[4]。
从宏观方面,工件在周期性外载的作用下,工件各部产生的交变动应力与内部残余应力相互叠加,在应力较高的区域,产生了微小的塑性变形,使残余应力峰值下降,改变了工件原有的内应力场,最终使工件的残余应力降低并重新分布,在较低的应力水平下达到平衡。工件局部发生永久塑性变形,提高了材料抗变形能力。
从微观方面,根据能量原理,较小的间隙原子优先处在位错旁的空洞里,它们起着钉住位错,阻碍位错滑移的作用。当振动时效提供足够大的动应力时,将使金属材料内部的位错滑移产生微观塑性变形,使残余应力得以释放,并且提高了工件抗变形能力。
2 振动时效技术工艺的制定及实施
2.1 溪洛渡筒阀的制造
溪洛渡筒阀阀体的外直径为Φ9910mm,而壁厚仅为200mm,由电液同步装置进行同步控制,采用6 个接力器操作阀体上下运动,阀体采用高强度钢板制造,本体材料为S355Jo,上下端部长200mm 范围镶焊不锈钢板。由于运输尺寸限制,分为两瓣制造,两瓣阀体采用高强度螺栓连接,分瓣面外部封焊以防止漏水和变形,在分瓣面两侧的筒体上交错布置把合螺栓所需要的小窗口,阀体把合后将小窗口封焊。阀体在工厂内分两瓣下料,每瓣由两个组块组焊而成,在工厂内精加工各瓣阀体的合缝面及焊接坡口,对阀体的其它部分进行粗加工后分两瓣运输至工地,两瓣阀体在工地焊接成整体,并在工地进行热处理和精加工。
2.2 大型筒阀振动时效工艺
溪洛渡筒阀阀体是大直径薄壁结构,刚度相对较小,内部存在的残余应力在运输及加工过程中将使筒阀产生变形,给后续的精加工和工地现场装配带来不利的影响。为了保证精加工尺寸精度,使筒阀在加工过程中所产生的应力变形控制在一定范围内,采取在筒阀粗加工之后加入振动时效消除残余应力的生产工序,以保证筒阀最终组圆精加工的尺寸精度。根据筒阀的环形结构,依据JB/T 5926-2005《振动时效效果 评定方法》标准要求,对筒阀进行振动时效工艺分析与调整,分析不同频率下的振动时效效果,制定筒阀的最佳振时效工艺。溪洛渡筒阀阀体结构示意图如图1所示。
筒阀采用亚共振振动时效模式,两瓣阀体采用螺栓把合的方式实现整个筒阀阀体的组圆。振动时效过程采用四点弹性支撑,为了防止地面对工件振动产生阻尼作用,支撑部分由橡胶垫和方箱构成,四点相隔90°均匀分布,而且,支撑点避开合缝面和焊接部位。激振点(激振器)放置相邻的两个支撑点中间位置,采用C 型夹将激振器固定到筒阀上。拾振点(拾振器)固定在筒阀两支撑点间振动幅度相对较大的位置。根据激振器激振频率调整激振器的偏心大小,确定相应转速所对应的激振频率,时效时间为12~20min,筒阀振动时效工艺示意图如图2 所示。
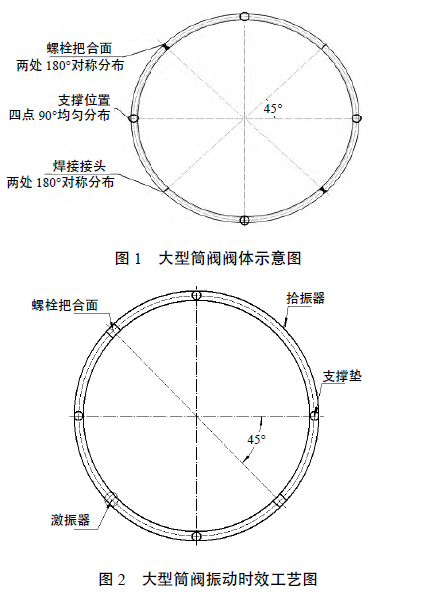
2.3 大型筒阀振动时效工艺特点
筒阀为圆环形结构,适合采用亚共振时效方法,通过对筒阀振动时效全过程的分析,确定了大型筒阀振动时效工艺特点:
(a)共振峰对激振力的大小比较敏感,过大的激振力造成设备过流保护,稍小的激振力则达不到足够的振幅要求而影响时效效果。因此,可通过调整激振器位置和微调偏心的方式加以解决。
(b)共振峰带宽较窄,自动时效模式下选取亚共
振频率时容易选取到较低振幅,而不能获得足够的激振力,这种现象在筒阀这类结构件中非常容易发生直接影响工件的消应力效果。为了保证时效效果,可通过手动调节方式对转速进行调节,保证时效加速度在共振频率产生最大加速度的2/3 左右,以获取足够的激振能量,但同时要避免选取的激振频率过大而产生过时效,而对工件造成不利影响。
3 大型筒阀振动时效效果判定
筒阀消除残余应力的主要目的是控制加工过程中的变形,以及保证后续装配过程中的尺寸精度。因此,为了对振动时效对筒阀的消除残余应力效果进行分析和判定,首先要确定振动时效是否达到筒阀稳定尺寸精度的要求,其次要满足JB/T 5926-2005《振动时效效果评定方法》中振动时效参数工艺曲线的要求,为筒阀振动时效工艺是否满足要求提供依据。
3.1 参数曲线判定法
振动时效参数曲线判定是振动时效效果评判的重要依据之一,该方法是根据时效曲线(a-t 曲线)和振前振后扫频曲线(a-n 曲线)的变化来判定振动时效效果。因为在振动时效过程中,随着残余应力的下降,工件的内阻尼减小,所以在幅频特性曲线上所表现出的是固有频率、共振峰值和频带等参数发生变化。由于参数曲线的监测比较容易实现,既可以通过振幅的变化来控制振动时效处理的有效时间,又可以通过参数变化量来监测残余应力的变化情况,所以参数曲线判定法是国内外普遍采用的一种较为成熟的方法。
在大型筒阀实际的亚共振时效曲线中,a-t 曲线下降后变平,a-n 曲线振后加速度峰值比振前升高,并且相比振前发生了移动。说明筒阀在振动时效过程中残余应力得到了释放,达到了JB/T 5926-2005《振动时效效果评定方法》标准要求的振动时效工艺效果。
3.2 工件尺寸稳定性检测法
振动时效效果评定方法中,对于需要满足加工尺寸精度的工件,最为直观的判断方法就是测量工件尺寸是否满足生产使用的要求。尺寸精度稳定性是根据定期对工件尺寸精度的测量来实现的。它包括两方面内容:一方面是观测工件尺寸精度随时间而发生的变化量,与精度允差相比较;另一方面是观察工件在静、动载荷作用后的尺寸精度变化量,以鉴定振动时效工艺的时效效果。振动时效后,残余应力消除和均化的效果好,工件中残余应力的再分布的可能性和程度就比较小,工件的尺寸精度稳定性就好。大量实践证明,在保持工件尺寸精度稳定性方面,振动时效技术比其他传统的时效方法更具有明显的优势。大型筒阀不仅在加工过程中容易产生变形,在经过多次的吊装、翻转后,较高残余应力也会导致工件的变形,并对最后精加工的尺寸造成超差的影响。为了验证振动时效对筒阀尺寸精度的稳定性作用,对筒阀最后精加工完成的尺寸进行了测量统计,以判断振动时效是否达到了预期效果。
4 结论
通过参数曲线判定、尺寸稳定性测量方法的验证以看出,振动时效技术在控制大型筒阀加工过程中的变形,以及稳定尺寸精度方面的应用是成功的,取得了非常好的效果,满足了精加工设计尺寸及装配尺寸精度的要求,有效解决了大型筒阀这类大直径薄壁圆筒结构件的机械加工变形问题,提高了超大型筒阀的加工质量和生产效率。