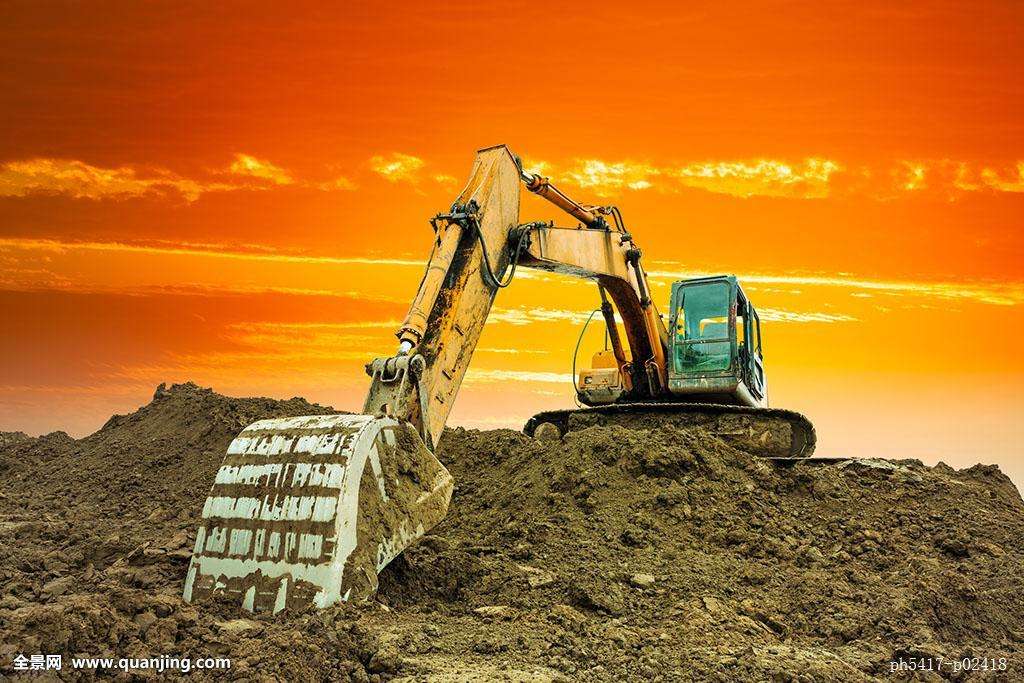
挖掘机的底盘、平台、动臂和斗杆等均是焊接结构件,焊接后必然会有残余应力,残余应力是导致其变形或者开裂的重要原因,因此有必要对这些工件进行消除残余应力的时效处理。时效有自然时效、热时效和振动时效3 种基本工艺方法。自然时效是将工件在室温条件下放置一年左右,自然释放其残余应力;热时效是将工件放置在电炉中,在约600 ℃保温5 h 左右随炉缓冷以消除残余应力;振动时效是使用振动设备,对工件施加0.5 h 左右的亚共振振动,达到消除残余应力的目的。
自然时效由于时效周期太长,不能满足生产进度要求,不可能应用;热时效设备投资较大,时效成本很高,生产效率较低,应用有难度;振动时效设备投资少、生产效率高、时效成本低,是最为理想的时效方式。
1 振动时效技术
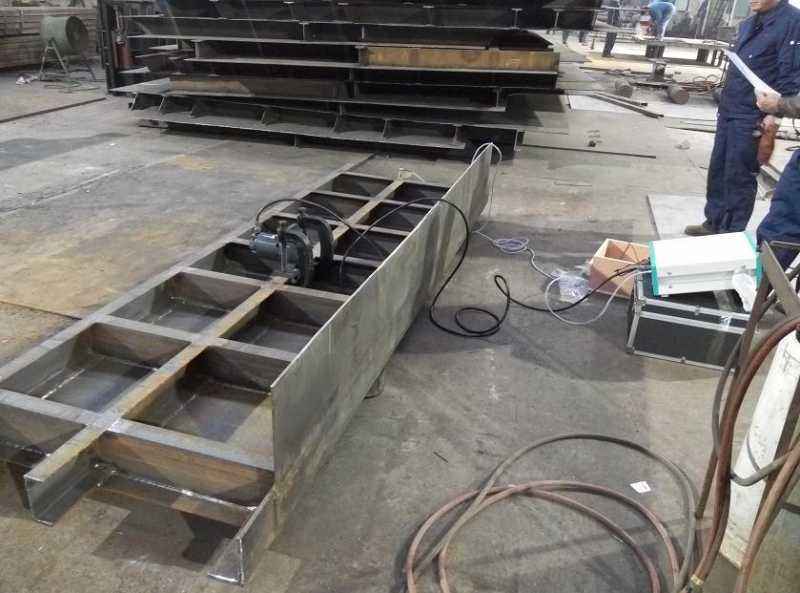
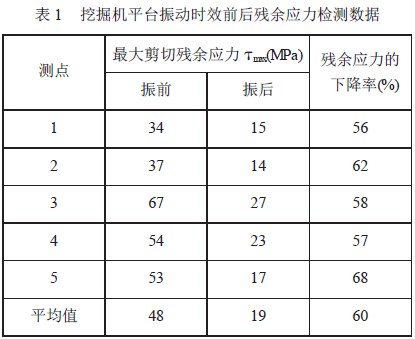
3 振动时效的工艺管理和经济效益
1 振动时效技术
1.1 振动时效技术的原理和设备
振动时效是使用振动时效设备,对金属工件施加30 min 左右的亚共振振动,以降低和均化残余应力,防止应力变形或者开裂的革命性时效高新技术,广泛用于对铸件和焊接件的时效处理。振动时效的工艺过程很简便。首先用胶垫支撑好工件,然后将激振器和测振器固定在工件上,就可以开机进行振动时效处理了。如果采用全自动工艺,先是振前扫频搜寻共振峰,找到共振峰后,设备将自动优选最佳亚共振点进行共振时效半小时左右,并自动进行振后扫频和打印时效曲线作为质检依据。振动时效消除残余应力的基本原理是这样的在数万次亚共振振动过程中,工件已经产生了最大程度的微观塑性变形,而且变形已趋稳定,残余应力已经释放,处于平衡状态。从振动的动应力分析,在振动时效时,工件会受到一个交变动应力作用,这个动应力与残余应力叠加,达到一定数值后,在应力集中最严重的部位,就会超过屈服极限而产生塑性变形,从而降低了该处的残余应力,而后振动又在另处应力集中较严重的部位产生同样作用,直到不能引起任何部位的塑性变形为止。因此,振动时效可以将残余应力集中现象消除,使残余应力处于平衡状态,从而能有效防止应力变形或者开裂。振动时效设备是成功地应用振动时效技术的基本条件。
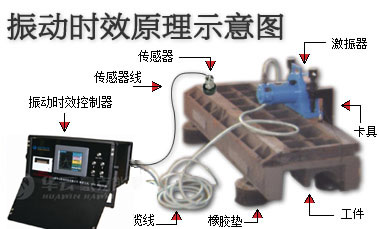
1.2 振动时效工艺的实施
某工程机械公司生产的小型挖掘机的底盘、平台、动臂、斗杆等焊接结构件,均采用华云HK系列振动时效设备进行振动时效处理。其中底盘和平台比较大的工件,可以单件进行振动时效处理,动臂和斗杆比较小的工件,原来也曾经试用单件振动时效处理,但是其固有共振频率很高,振动时效的声音很大,激振器在高转速状态下运行也容易出现故障,因此改用振动平台进行批量振动时效处理,大大降低了工件有共振频率和振动时效时发出的噪声。
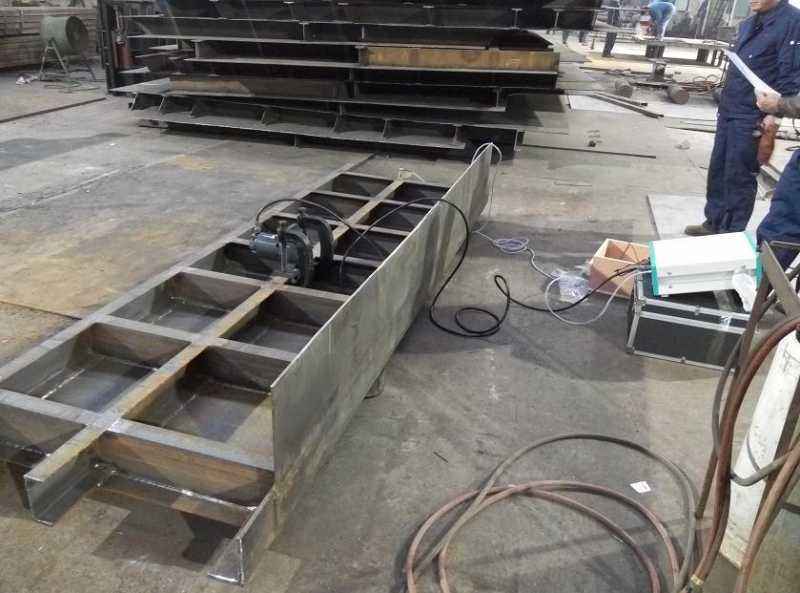
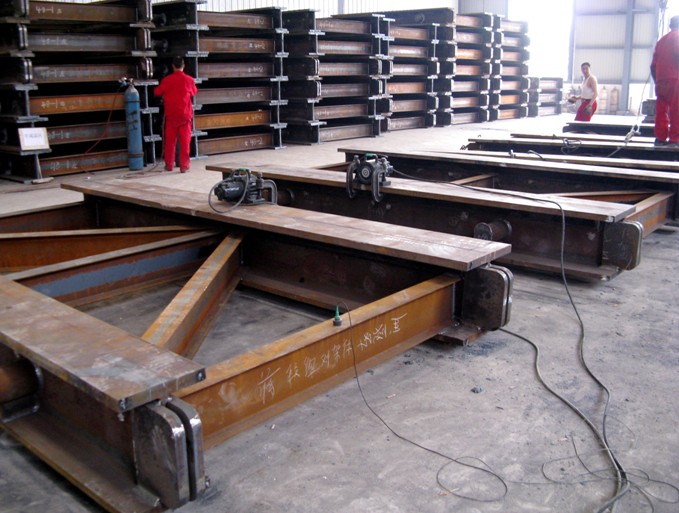
2 振动时效工艺的效果
为了了解振动时效的工艺效果,我们从振动时效前后残余应力检测、振动时效工艺曲线和振动时效工件的实际使用效果等方面进行了综合考察。结果表明振动时效的工艺效果相当好。
2.1 振动时效前后残余应力的检测
为了定量了解振动时效工艺效果,使用磁测应力仪,检测了挖掘机平台等工件焊缝处振动时效前后的残余应力。测量结果表明,挖掘机平台在振动处理前,焊缝处残余应力集中现象较严重。在焊缝中心区域应力较高,最大剪切残余应力值约为54~67 MPa,已经接近了许用安全剪切应力,为不安全的残余应力。在焊缝非中心区域应力较低,约为30~50 MPa。经振动时效处理,焊缝处残余应力集中现象已消除,焊缝中心区域和非焊缝区域,应力值已相近,峰值残余应力已经从60 MPa 左右,下降到25 MPa 左右,下降率约为60%,远小于许用安全剪切应力,平台处于安全的低应力平衡状态。表1 及图2 分别为挖掘机平台振动时效前后残余应力检测数据和应力分布曲线。
2.2 振动时效工件的实际使用效果
公司从2000 年起应用振动时效技术5 年多来累计约有5 000 台挖掘机产品的焊接结构件都进行了振动时效处理,此外公司是通过ISO9001:2000 认证的企业,对产品的质量都有一套跟踪检查制度。在没有应用振动时效技术之前,底盘、动臂、平台和斗杆焊接件的变形和开裂质量问题时有出现,应用振动时效技术之后,这个质量问题完全解决了,可见振动时效的实际使用效果是很好的。
3 振动时效的工艺管理和经济效益
在实际生产上,公司是通过振动时效工艺曲线来检测振动时效效果的。每振动时效处理一个工件,都必须要有相应的振动时效工艺曲线,这个工艺曲线,要经过质量检验部门依据工艺部门制订的振动时效工艺卡的标准曲线进行验收,如果达不到验收标准,还要返工重振。验收合格后工件才能转到下一工序,有效地保证了振动时效工艺质量稳定可靠。
以下通过热时效和振动时效的费用比较来说明应用振动时效技术的经济效益。从2012 年开始公司累计振动时效处理了5 000台产品的焊接件,每台产品的焊接结构件平均质量约为1 t,总计处理了约5 000 t。公司购买了两套华云HK振动时效设备,设备购置费为10 万元,操作人员1 人(非专用),5 年该项工作累计工资额为8 万元,振动时效设备每天耗电量为10 度,每度电按照1.6元计,5 年累计使用电费为2.6万元。5 年累计振动时效的总费用为20.6万元。
以下通过热时效和振动时效的费用比较来说明应用振动时效技术的经济效益。从2012 年开始公司累计振动时效处理了5 000台产品的焊接件,每台产品的焊接结构件平均质量约为1 t,总计处理了约5 000 t。公司购买了两套华云HK振动时效设备,设备购置费为10 万元,操作人员1 人(非专用),5 年该项工作累计工资额为8 万元,振动时效设备每天耗电量为10 度,每度电按照1.6元计,5 年累计使用电费为2.6万元。5 年累计振动时效的总费用为20.6万元。
如果使用热时效,需要购买热时效炉,因为环境污染问题,不能使用燃煤热时效,只能使用电炉热时效。按照公司的产量,需要购买5 台100 kW的电炉,设备投资约100 万元,电炉的用电量很大,其综合热时效成本为500 元/t,处理5 000 t 工件,需要250 万元。5 年累计热时效的总费用需要350 万元。与热时效相比,振动时效可以节省多余300 万元的时效费用,此外,采用振动时效后与热时效相比所节省的大量工时尚未计算在内, 由此可见应用振动时效技术的经济效益是相当显著的。