焊接是船舶、飞机、汽车、火车、压力容器、起重设备等大结构、复杂结构的重要加工方法。由于在焊接接头处常常存在各类焊接缺陷、应力集中与拉伸残余应力,从而使接头处成为整个焊接结构的薄弱环节,因此焊接接头的质量对于焊接结构运行的可靠性和使用寿命起着决定性的作用。许多研究表明,焊接结构的失效尤其是疲劳失效大多起始于接头表面,因此对接头表面质量的优化可改善焊接结构性能,延长使用寿命。焊接接头表面质量不仅包括接头几何形状(如余高、焊趾过渡角及过渡半径等)、粗糙度、表面缺陷(气孔、咬边、裂纹等)等表面形貌特征,也包含接头表面的残余应力、显微硬度、塑性变形、组织形态等特征。
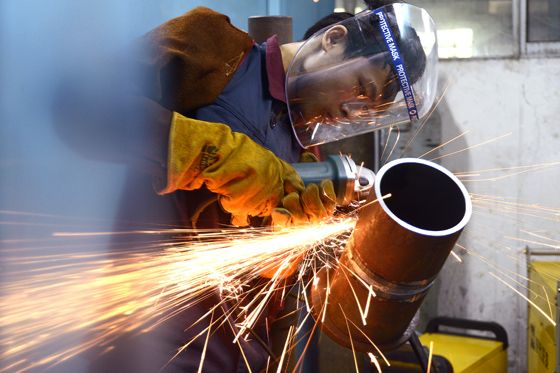
1 、超声冲击对焊接接头表面几何形状的影响
焊接工艺产生的接头余高会引起构件接头截面形状突变,导致突变处的应力集中较大,尤其是焊趾部位表现更为突出,对接头性能产生不利的影响。另外,焊缝金属与母材金属间的表面过渡连接形状对接头性能也有重要影响。超声冲击可以改善焊接接头的表面形貌。经过超声冲击处理,改变了原始焊态接头表面的鱼鳞纹状的形貌特征,焊接接头的表面变得相对平坦。在母材与焊缝连接处可以形成形状相对良好、连续而且均匀的圆弧过渡,同时过渡圆弧的半径变大。接头应力集中是决定焊接接头性能的重要因素。焊趾应力集中程度越大,越容易产生裂纹,接头强度也就越低。通常情况下,可以通过应力集中系数对接头的应力集中程度来进行表征。研究与实验表明,在接头类型和有效尺寸一定的条件下,焊接接头处应力集中系数的大小主要与接头表面的几何数有关。以对接接头为例,其接头应力集中系数的大小主要取决于焊缝余高和焊趾区的过渡半径以及夹角。在一定范围内,减小余高和焊缝向母材的过渡角、增加焊趾区过渡半径,都会使应力集中系数减小,从而使缺口效应也减小。
对 16Mn 钢焊接接头进行超声冲击的试验表明,接头处的过渡半径从原始焊态的0.2~0.4 mm 增加为超声冲击之后的1.6~2.0 mm;十字接头和对接接头的有效应力集中系数分别比原始焊态下降了25%和23%。TC4 钛合金焊接接头在经过超声冲击处理后,接头处的过渡半径从原始焊态的0.12~0.96 mm增大到1.3~3.3 mm,有效应力集中系数下降了近32.0%,由4.1 减小为2.79。Q370qE 钢焊接接头经超声冲击处理后,焊缝宽度变化不明显,余高有所降低,焊趾区过渡半径明显增大66%,过渡角由38°减为27°。超声冲击处理把超声频的机械振动传递给焊接接头,使接头表面产生一定深度的塑变层,使余高变小,同时可通过冲击头的冲击调整焊趾与母材连接处的过渡,使焊趾角与焊趾半径增大,进而降低了应力集中程度。增大过渡半径和减小过渡角使焊趾平滑过渡是超声冲击改善接头表面形貌、降低应力集中的主要表现形式。
2 超声冲击对焊接接头表面残余应力的影响
对 16Mn 钢焊接接头进行超声冲击的试验表明,接头处的过渡半径从原始焊态的0.2~0.4 mm 增加为超声冲击之后的1.6~2.0 mm;十字接头和对接接头的有效应力集中系数分别比原始焊态下降了25%和23%。TC4 钛合金焊接接头在经过超声冲击处理后,接头处的过渡半径从原始焊态的0.12~0.96 mm增大到1.3~3.3 mm,有效应力集中系数下降了近32.0%,由4.1 减小为2.79。Q370qE 钢焊接接头经超声冲击处理后,焊缝宽度变化不明显,余高有所降低,焊趾区过渡半径明显增大66%,过渡角由38°减为27°。超声冲击处理把超声频的机械振动传递给焊接接头,使接头表面产生一定深度的塑变层,使余高变小,同时可通过冲击头的冲击调整焊趾与母材连接处的过渡,使焊趾角与焊趾半径增大,进而降低了应力集中程度。增大过渡半径和减小过渡角使焊趾平滑过渡是超声冲击改善接头表面形貌、降低应力集中的主要表现形式。
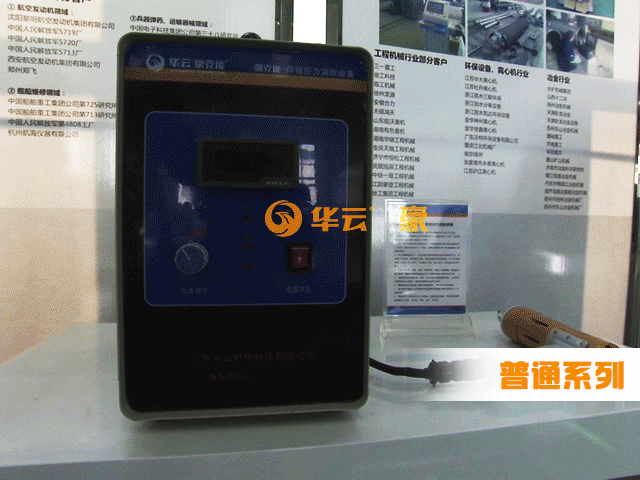
2 超声冲击对焊接接头表面残余应力的影响
焊接后的接头在三维空间产生冷却收缩,因此在接头中也应存在3 个方向的残余应力。在厚度相对较小的焊接结构中,厚度方向的残余应力很小,一般不予考虑,因此在超声冲击试验研究中,一般只考虑由于焊缝纵向收缩而形成的纵向残余应力和垂直于焊缝方向产生的横向残余应力。一般而言,残余拉应力对焊接结构的性能(尤其是疲劳性能)产生不利影响,而残余压应力往往是有利的。由于在焊接接头中可能既存在残余拉应力又存在残余压应力,倘若能将残余压应力调整到位于接头表面或应力集中区,就会非常有利;如果在接头表面或应力集中区存在着残余拉应力,则应想方设法消除。超声冲击过程是高频能量和冲击应力作用于焊接接头表面,使其产生塑性变形,从而在接头内残余应力的高峰处产生局部的屈服而迫使应力峰值降低的过程。伴随着冲击过程的持续进行,在接头表面和次表面内产生有益的残余压应力。许多学者对超声冲击调整接头残余应力场进行了研究。
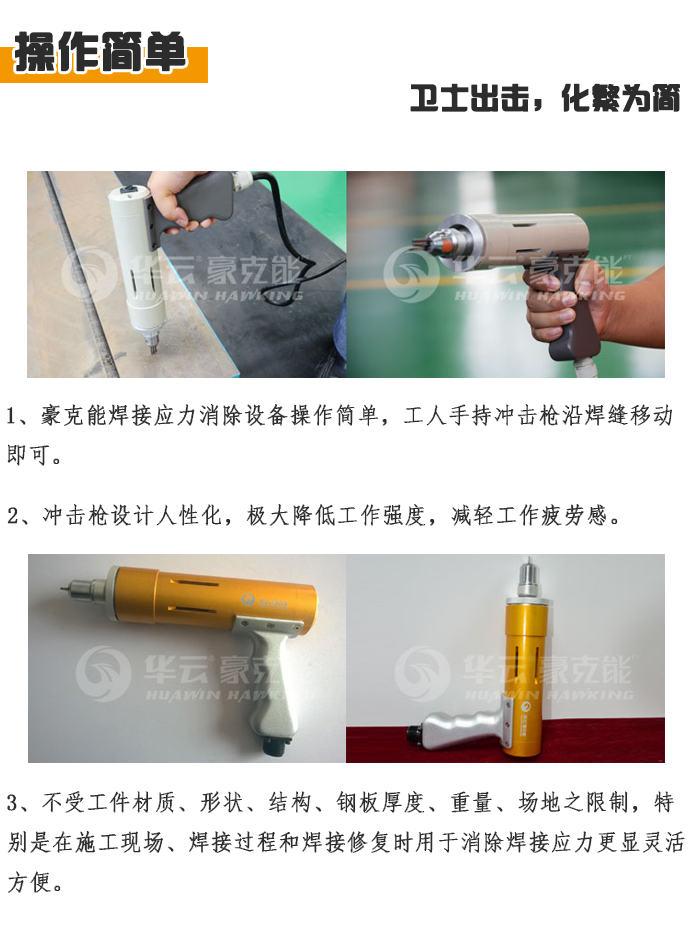
饶德林等对Q235 钢埋弧焊接头全范围冲击和焊趾冲击2 种超声冲击工艺的对比试验表明,超声冲击能够在焊接接头表面形成较高的压应力以抵消焊接过程产生的拉应力;对接头处的冲击不但影响了接头表面,使其产生残余压应力,而且也影响了邻近的热影响区,使得热影响区的残余应力降低。吕宗敏等研究表明,16MnR 焊接接头焊趾表面经超声冲击后在不同方向残余压应力的变化不同:在冲击时间为6 min 时纵向残余压应力达到最大值,延长冲击时间,表面残余压应力减小并在接近最大值的1/2 处趋于稳定;随着冲击时间的延长,横向残余压应力增大,在冲击时间为3 min 时残余压应力达到最大值,随后焊趾表面残余压应力呈阶梯式降低。李进一等建立了AISI304 奥氏体不锈钢板材超声冲击残余应力场的三维有限元模型,分析表明,冲击速度和冲击针头直径的变化与残余应力及应力层深度的变化具有明显的正相关,并且随着冲击次数的增加,残余压应力层深度增厚,但形成的最大残余压应力值减小。关于超声冲击处理对焊接接头残余应力的影响机制,多数研究者认为是由于宏观塑性变形引起的微观位错运动与增殖所诱发。要完成由高能态的不稳定状态到低能态的稳定状态的转变,必然引发微观塑性变形,从而使得焊接接头处的残余拉应力得以释放、降低或消除。
3 超声冲击对焊接接头表面组织形态的影响
对普通低碳钢、高强钢、铝合金、钛合金等焊接接头超声冲击处理的试验表明,剧烈的塑性变形使冲击区金属表层的显微组织发生了显著变化,晶粒尺寸明显减小,形成了细晶强化层。如22SiMn2TiB超高强钢焊接接头超声冲击处理后,组织细化层深达到50 μm,表层晶粒尺寸平均值在63~82 nm 范围;
16MnR 焊接接头焊趾经超声冲击处理后,在焊趾及其附近表面区域获得100 nm 以下的纳米组织,晶粒趋向呈随机分布。2A12 铝合金焊接接头经超声冲击处理后,接头的熔合区变窄,并形成了致密的塑变层,塑变层深达300 μm(距接头表面),同时产生了平行于接头表面的宏观织构,显微组织细化。
超声冲击焊接接头表面晶粒细化的实质是超声冲击处理诱发接头表面发生剧烈塑性变形,使大尺寸晶粒“碎裂”并形成细小晶粒的过程。这种“碎裂”是在位错、孪晶等不同的微观变形方式下逐渐进行的,先是在大尺寸晶粒内部转变成小角亚晶界,然后小角晶界继续吸收位错逐渐发展成大角晶界,如此循环往复,从而碎化成小晶粒的过程。在超声处理工艺及参数一定的情况下,接头的塑性变形方式和晶粒细化机理主要与其层错能和滑移系数目有关,二者的差异决定了不同材料晶粒细化的具体过程。
4 超声冲击对焊接接头显微硬度、粗糙度及表面缺陷的影响
原始焊态接头的焊缝区、热影响区及母材区的显微硬度虽有差异,但各区域硬度沿厚度方向的变化均比较平缓。但是经超声冲击处理后,焊接接头表层形成了一层致密的塑性变形层,并产生加工硬化效应,整个焊接接头的表层及次表层显微硬度得到了显著的提高,而且硬度沿厚度方向呈梯度变化。李东等对J507 堆焊层及SS400 钢对接接头超声冲击处理前后显微硬度的变化进行的测定表明,表面细晶层比中心区域的显微硬度提高约1.4 倍。陈芙蓉等研究表明7A52 铝合金焊接接头经过超声冲击处理后,与未处理相比热影响区与焊缝区的最高显微硬度提高了21.5%。在接头部位存在着许多不同类型的缺陷,导致疲劳裂纹早期开裂,使性能急剧下降。
焊接缺陷大体上可分为两大类:面状缺陷(如裂纹等)和体积型缺陷(气孔、夹渣等)。焊接缺陷对接头性能的影响与缺陷的种类、方向和位置有关。超声冲击引起的塑性变形还可以改善焊接接头焊缝中的部分表面微缺陷(未焊透、咬边、气孔、缩松、微裂纹等),同时引入残余压应力,改变了裂纹形核机制,从焊趾处的表面形核演变为次表面形核,减少了焊趾表面开裂。尽管超声冲击处理具有以上优点,但经UIT 处理后的接头表面多数情况下会因冲击形成的塑性压痕使被处理工件表面比较粗糙[50],并且塑变层深度并不会随超声冲击强度的提高而无限增加;冲击强度相对较高时,接头表层开始出现微观缺陷(表面微裂纹等),使表面质量劣化。尹丹青的研究也证实了以上观点:原始焊态接头中的疲劳裂纹主要起源于焊趾表面或次表面的夹杂物处。超声冲击处理态的接头,裂纹部分起源于夹杂物或夹渣微小缺陷,部分起源于由于超声处理的冲击挤压作用造成的表层或次表层微裂纹。
焊接缺陷大体上可分为两大类:面状缺陷(如裂纹等)和体积型缺陷(气孔、夹渣等)。焊接缺陷对接头性能的影响与缺陷的种类、方向和位置有关。超声冲击引起的塑性变形还可以改善焊接接头焊缝中的部分表面微缺陷(未焊透、咬边、气孔、缩松、微裂纹等),同时引入残余压应力,改变了裂纹形核机制,从焊趾处的表面形核演变为次表面形核,减少了焊趾表面开裂。尽管超声冲击处理具有以上优点,但经UIT 处理后的接头表面多数情况下会因冲击形成的塑性压痕使被处理工件表面比较粗糙[50],并且塑变层深度并不会随超声冲击强度的提高而无限增加;冲击强度相对较高时,接头表层开始出现微观缺陷(表面微裂纹等),使表面质量劣化。尹丹青的研究也证实了以上观点:原始焊态接头中的疲劳裂纹主要起源于焊趾表面或次表面的夹杂物处。超声冲击处理态的接头,裂纹部分起源于夹杂物或夹渣微小缺陷,部分起源于由于超声处理的冲击挤压作用造成的表层或次表层微裂纹。
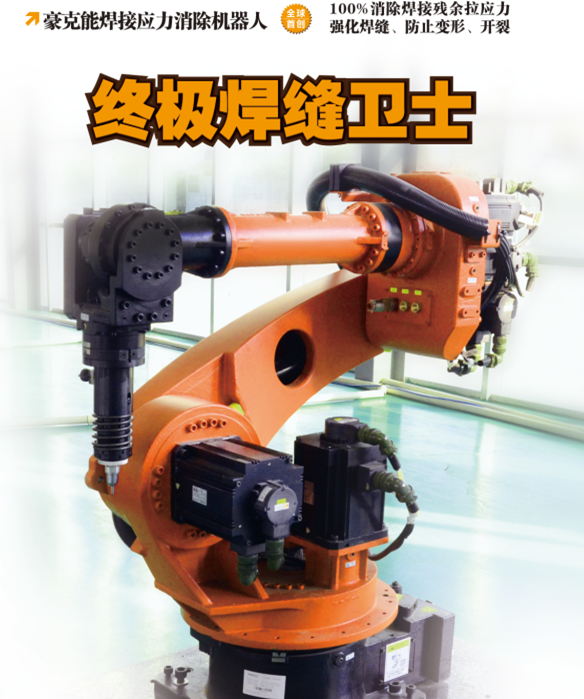
5、总结与展望
超声冲击工艺作用于焊接接头不仅能够改善接头表面的几何外形、降低接头处的应力集中程度;还能调节接头及其附近的残余应力场,在接头表面形成对接头性能有益的压应力;同时又能使接头表层组织细化,消除部分焊接微缺陷,提高焊接接头的性能,并且设备轻巧、使用方便、效率高、成本低,适用于各种接头各种场合。