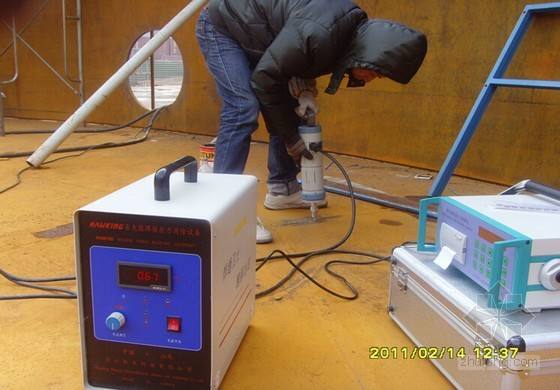
在焊接过程中,焊接技术本身存在的集中加热和快速冷却过程以及添加不同的焊接材料,都会造成焊接接头组织及性能的不均匀,这种不均匀使焊接接头成为构件的薄弱环节和易失效区域。如何使焊接接头组织及性能均匀化,提高焊接接头的强度、硬度、抗疲劳断裂、耐腐蚀等性能,已经得到许多焊接研究者的重视。通过对材料进行表面改性处理,如热处理、化学处理及机械处理,可以提高材料的抗疲劳性能。目前,许多研究者采用高能喷丸、表面机械研磨处理、超音速微粒轰击、超声冲击、激光冲击等方法对焊接接头进行表面改性处理,使焊接接头表面晶粒得到细化,其力学性能也得到不同程度的改善。
豪克能超声冲击改性处理是通过结合超声频机械振动和传统表面压光工艺进行工作的。超声冲击的工作原理是将超声冲击工作头垂直于工件表面,在一定静压力和进给速度作用下,冲击头将压力和超声冲击振动传递给处于旋转状态的机械零部件表面,使材料表面产生弹、塑性变形。
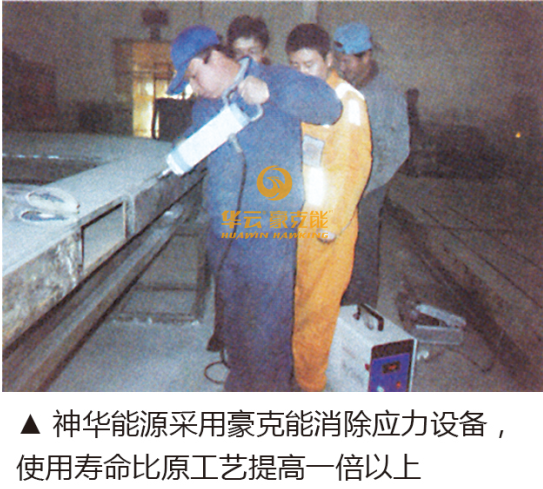
李东等人对J507 堆焊层进行超声冲击改性处理,并对超声冲击处理前后表面层显微组织和显微硬度的变化进行了分析。发现在超声冲击作用下,粗晶粒内部形成了高密度的位错墙和位错缠结,在不断的冲击作用下逐渐演变成小角度亚晶界,继续吸收位错进而转变成大角度晶界,上述过程不断重复,晶粒尺寸就不断减小,最终形成纳米级的晶粒,同时表面纳米晶层比中心区域的显微硬度提高1. 4 倍。为了研究超声冲击工艺对Q235 钢结构箱型柱焊接残余应力的影响,饶德林等人对埋弧焊焊缝进行了超声冲击改性处理,并分别采用了全覆盖冲击和焊趾冲击两种冲击工艺进行分析试验。超声冲击工艺可以使焊缝表面产生较高的压应力,而对焊趾的冲击不但使焊趾表面产生压应力,同时也降低了焊缝的残余应力。
综合许多研究可以看出,超声冲击改性处理能够提高材料的疲劳强度,延长材料的疲劳寿命。除此之外,对焊接接头进行超声冲击改性处理也可以大幅提高其疲劳强度,使疲劳寿命增加十几倍以上。为了研究超声冲击提高焊接接头疲劳强度的机理,王东坡等人对超声冲击处理前后焊趾区的几何形状及硬度的变化进行了测量,并研究了超声冲击造成的焊趾区几何形状变化及残余压缩应力对接头疲劳性能改善的影响行为。对于低中强钢来说,超声冲击处理焊接接头疲劳性能的改善主要源于焊趾部位形成的残余压应力及改善焊趾几何外形这两个因素,硬化的作用相比次之。研究还证明,超声冲击处理通过增加焊趾区过渡半径,使得焊接接头应力集中程度降低。
李占明等人对2A12 铝合金焊接接头进行了超声冲击处理,发现超声冲击处理可以使焊缝表面形成深度约300 μm 左右的塑性变形层,处理层的晶粒平均尺寸为123 nm,平均微观应变为0.134%。
通过超声冲击处理,发现焊缝中气孔、缩松等缺陷明显减少,焊接接头表面和断面显微硬度明显提高,同时消除了焊接接头表面残余拉应力,形成了最大约为- 285 MPa 的残余压应力。除此之外,超声冲击处理使2A12 铝合金焊接接头疲劳强度由40.5 MPa 提高到56.1 MPa,提高了38.5%。
叶雄林等研究了超声冲击处理对22SiMn2TiB钢焊接接头疲劳性能的作用,分析了处理前后样品的残余应力分布,并对疲劳样品断口形貌进行了观察分析,确定了裂纹形核机制。他们发现超声冲击处理可以延长22SiMn2TiB 钢焊接接头的疲劳寿命。超声冲击处理改变了裂纹形核机制,从焊趾处的表面形核演变为次表面形核,而超声冲击处理消除了焊趾处的微缺陷,并引入残余压应力,减少了焊趾表面开裂,使得焊接接头具有更长的疲劳寿命。
豪克能超声冲击设备具有操作简单、方便灵活的特点,对一些结构复杂的焊接接头也能够进行表面改性处理,可以适应于各种施工工况,因此超声冲击表面改性处理方法应用比较广泛,不仅适用于钢结构,还在铝合金、钛合金及镁合金等材料的焊后处理中具有广泛的应用。
豪克能超声冲击设备具有操作简单、方便灵活的特点,对一些结构复杂的焊接接头也能够进行表面改性处理,可以适应于各种施工工况,因此超声冲击表面改性处理方法应用比较广泛,不仅适用于钢结构,还在铝合金、钛合金及镁合金等材料的焊后处理中具有广泛的应用。