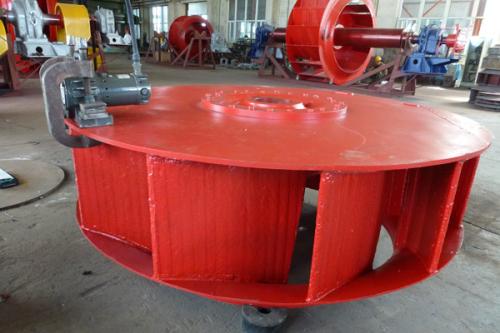
一、前言
与常规热时效工艺技术相比,振动时效工艺技术以其设备成本低、便于操作、不受场地限制、时效时间短、耗能少、污染少等优点,受到国内外机械制造业的广泛重视。我公司经过多年的调研、试验和验证,终于完成了振动时效技术在大型轴流压缩机机壳(铸件)、TRT 机壳(铸件)、离心压缩机机壳(铸件)、轴流压缩机底座(焊接件)、离心压缩机底座(焊接件)、烧结类离心鼓风机叶轮(焊接件)等产品消应力中的应用。现已持续稳定地应用在风机产品制造中,满足了产品的制造质量要求,取得了良好的经济效益。
二、振动时效的基本机理
热加工结束后,工件会存在相互平衡的内应力,即残余应力。在冷加工时,由于工件受到装夹应力和切削应力的作用,使得工件加工表面部分发生应变,部分应力释放,产生新的内应力分布,造成新的残余应力。在宏观状态下,工件的外形尺寸会发生微量变化,这表现工件精加工尺寸超差,从而影响了产品的制造质量。同时,由于残余应力的存在,会使工件在运转过程中发生蠕变;加
剧应力腐蚀,降低工件的疲劳极限,从而影响工件的使用寿命,因此在鼓压风机生产制造过程中必须尽可能地降低工件残余应力。振动时效又是如何消除工件中残余应力的呢?目前,对振动时效原理达成一致的观点就是把工件用橡胶垫支起,将振动时效装置固定在工件上,在可控制状态下,激振器在工件的几个共振频率处振动,并持续一段时间,对工件施以激振应力!动。激振应力!动是一种交变应力,在某一时刻工件内应力集中的某一局域,激振应力!动与残余应力!残的叠加应力将会大于材料的屈服极限,使得被处理点出现局部微观的塑性应变。由于应变的释放使残余应力得以下降,即当!动+!残>!!时,则残余应力被部分消除。当!动+!残!!!时,则残余应力将不再变化。在工序间,对工件进行的振动时效处理,使工件内的残余应力部分得到了消除和调整。
三、振动时效工艺在风机产品中的应用
在振动时效处理工艺中,首先要考察工件的结构刚性,初步分析工件可能出现的振动波形,以确定工件橡胶垫的支撑位置及激振点等工艺参数。其次要根据工件的重量、材质及工件应力来选择激振应力
振动时效处理后,由于消除了工件内部分残余应力,引起了工件处理前后振幅一频率(时间)曲线的变化。振动时效后工件的振幅—频率(时间)曲线左移,峰值升高,峰形变窄,此后再进行振动时效残余应力将不再变化,振幅—频率(时间)曲线亦不再变化,见图1。因此,用振幅—频率(时间)特征曲线来作为检测振动时效处理效果的检验依据。振幅—频率(时间)特征曲线监测法是国内外普遍采用的较为成熟的振动时效工件残余应力的测试方法。
(1)在轴流压缩机、TRT 装置和离心压缩机铸造机壳上的应用。
产品名称:AV45 - 17 轴流压缩机机壳
材质:HT 250,重量:9513kg
外形尺寸:4554 X 2430 X 1100
时机:半精加工前
激振设备型号:ZSK - 06B 型
支撑:橡胶垫四点支撑
激振器的装卡、拾振器的位置及支撑位置见图2、图3。
偏心挡位:26%
扫描频率:Ngm = 6159r / min
激振频率:Nt = 6077r / min
加速度:G = 17 . 2 ~ 21 . 2m / S2
时间:30min,手动控制处理
振后扫描频率:Ngm = 6047r / min
实践表明,振动时效处理后的机壳各加工面尺寸精度、安装精度满足了设计要求,取得了较好的经济效益。
图2 机壳振动时效装置装卡示意图
图3 机壳振动时效装置装卡示意图
(2)振动时效在压缩机的焊接底座上的应用。
产品名称:压缩机组联合底座
材质:@235 - A,重量:8951kg
外形尺寸:9520 X 3030 X 1325
时机:焊接过程中和焊接完成后
激振设备型号:ZSK - 06B 型
支撑:橡胶垫四点支撑
激振器的装卡、拾振器的位置及支撑位置见图4。
偏心挡位:20%
扫描频率:Ngm = 3843r / min
激振频率:Nt = 3773r / min
加速度:G = 49 . 4m / S2
时间:15min,手动控制处理
振后扫描频率:Ngm = 3812r / min
实践表明,焊接过程中的振动时效和焊接后的振动时效,减少了焊接应力产生的变形,保证了底座各加工面尺寸精度满足设计要求,取得了较好的经济效益。
(3)在大型离心鼓风机叶轮上的应用。
产品名称:SJ8OOO 离心鼓风机叶轮
材质:l5MnV,重量:3334kg
外形尺寸:!253O X 746
时机:焊接完成后
激振设备型号:HB - 93 型
支撑:橡胶垫三点支撑
激振器的装卡、拾振器的位置及支撑位置见图5。
图5 叶轮盘类振动时效装置装卡示意图
偏心挡位:3O%
扫描频率:Ngm = 3774r / min
激振频率:Nt = 3732r / min
加速度:G = 44 . 8m / S
时间:l5min,手动控制处理,采用多点振动
振后扫描频率:Ngm = 3768r / min
实践表明,由于没有加热的影响,叶轮母材金相组织和表面成分未发生变化,同时,降低了叶轮的应力水平,提高了叶轮疲劳寿命。振动时效处理后的叶轮满足了设计要求,提高了叶轮运行可靠性,取得了较好的经济效益。
四、振动时效应用的经济效益分析
振动时效由于其设备价格低(与热时效炉比),设备易于搬运,可在施工现场进行时效处理,操作简便。因此,具有较好的经济效益。以每年平均振动时效处理铸件约7OO 吨,焊接件约5O 件
为基数,来计算比较振动时效与热时效经济效益,振动时效的费用仅为热时效费用的2 . 8%(见表l)。与热时效相比,振动时效基本上没有改变材料的常规机械性能;经振动时效处理的材料断裂
韧性 lc值比未经任何处理的要高;经振动时效处理的构件疲劳寿命的平均值比未处理件疲劳寿命的平均值约提高25 . 3%。说明振动时效可以用来提高焊接构件接头的疲劳寿命。对于高合金成份
的材料,进行热时效消应力处理仍具有其优点,热时效可促进材料金相组织的更进一步均匀化,提高材料金相组织的稳定性,避免材料蠕变大有好处;热时效也可促进材料氢的扩散,避免材料氢脆发生;同时,对于结构刚性较小振动时效无法进行的工件,热时效仍具有无法替代的特点。
在企业生产过程中,振动时效与热时效消应力只可以互为补充,不可以完全替代。只有发挥其各自特长来应用,才能发挥振动时效的经济效益和社会效益。