大部分印象中振动时效工艺仅对大件去除应力有效,那小零部件,几公斤甚至几百克的有没有作用呢?到底采用怎样的振动时效工艺采才能起到去除应力的目的呢?
残余应力对尺身尺寸精度稳定性有很大影响,主要表现为已经组装合格的游标卡尺,放置一段时间后,尺身长度方向会出现弯曲变形以及宽度方向出现扭曲变形,最终表现为测量误差超过游标卡尺的设计技术标准。据统计,由残余应力导致的游标卡尺产品不合格率,可达到10% 左右,经济损失很大。因此,有必要采取措施消除游标卡尺尺身残余应力。
残余应力对尺身尺寸精度稳定性有很大影响,主要表现为已经组装合格的游标卡尺,放置一段时间后,尺身长度方向会出现弯曲变形以及宽度方向出现扭曲变形,最终表现为测量误差超过游标卡尺的设计技术标准。据统计,由残余应力导致的游标卡尺产品不合格率,可达到10% 左右,经济损失很大。因此,有必要采取措施消除游标卡尺尺身残余应力。
1 技术方案
1.1 装置的结构及主要技术参数
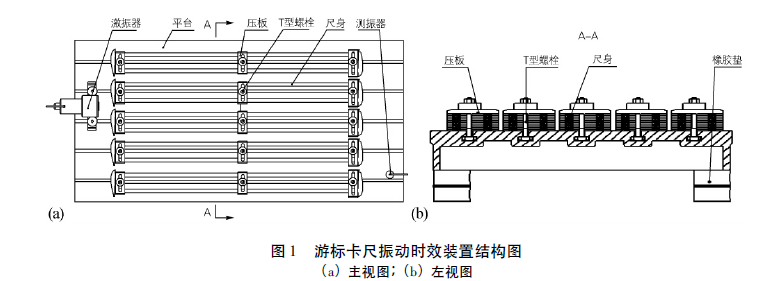
图1 所示游标卡尺振动时效装置主要包括: 1 个激振器、1 个测振器、4 个橡胶垫和1 个控制器,还有1 个铸件平台。该平台台面上设有5 条平行设置的T 型槽,平台的外形尺寸( 长× 宽× 高) 为3600 mm× 1200 mm × 200 mm,在T 型槽内设有多个T 型螺栓,每颗T 型螺栓外穿装有一块压板,4 个橡胶垫装在平台的下方与地面接触,激振器固定在平台一侧端部位置,测振器安置在与激振器对角的平台端角位置。图2 为游标卡尺振动时效装置实际现场图片。装置的主要技术参数为: 额定功率1. 2 kW,额定转速8000 r /min,额定激振力25 kN,具有全自动操作及快速检测效果的功能.
1.2 尺身装夹方法
游标卡尺尺身装夹固定在平台上,才能进行振动时效处理。其装夹方法是: 每组10 件沿厚度方向堆垛,然后首尾相连构成口字型,装在平台T 型槽的两侧,调整两组的间距便于装夹,每个T 型槽两侧均装有2 组尺身,两组尺身之间的T 型槽内装有T 型螺栓,设有通孔的压板分别装在两组尺身顶面靠近首端和尾端及中部的位置,平台T 型槽内的T 型螺栓分别依次穿装过尺身上的压板螺母,拧紧螺母把2 组尺身刚性固定在平台上,如图2 所示,总计装夹5 组尺身。对于3000 mm 长度的尺身,每次可以装夹100 件。
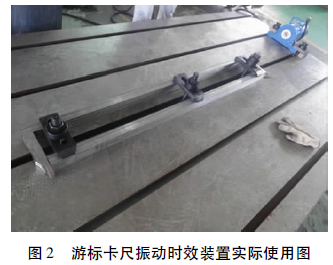
1.3 工艺过程
用该振动时效对游标卡尺尺身进行振动时效处理时,工艺过程是全自动的,具体如下: 启动全自动控制器,对装夹有游标卡尺尺身的平台进行振前扫频,当搜寻到低频共振峰后,选择该共振峰的亚共振点进行15 min 的振动时效处理,处理到设定时间后,自动振后扫频检测振动时效效果,并打印振动时效工艺曲线( 见图3) ,作为振动时效质检依据,振动时效处理结束。
振动时效原理
游标卡尺尺身固定在平台上后,与平台就构成了一个整体工件,该工件在一阶固有频率下进行15 min亚共振( 实际约为65 Hz) 振动时效处理,相当于尺身进行了约975 次的反复弯曲交变变形,残余应力就会降低并均匀化。游标卡尺尺身在装配和使用过程中都不会承受比共振振动更大的外力的作用,因此也就不会再出现变形。
对振动时效前后产品进行了对比统计( 见表1) ,产品合格率从90% 提高到了98% ,有效地解决了由残余应力导致的游标卡尺尺寸精度不稳定的问题
生产效率及成本
按照上述游标卡尺尺身装夹方法,处理长度为3000 mm 的游标卡尺尺身,每次装夹100 件,振动时效处理时间为15 min,装卸为35 min,总计时间为50 min,其生产效率为2 件/min,以每班工作时间8 h计算,每班可以处理960 件,每月22 个工作日,一年可处理253 440 件。振动时效操作员定员为2 人,其人工工资为240 元( 120 元/人) ,振动时效设备每班耗电量约为5 kW·h,合计电费为5 元,则振动时效生产成本为0. 26 元/件,可见游标卡尺的振动时效生产成本是极低的。对于更短尺寸的游标卡尺尺身,振动时效的生产效率更高。因此该装置可满足大批量、多品种和多规格的游标卡尺的振动时效处理要求。
经济社会效益
经济社会效益
如上所述,使用该装置对卡尺尺身进行振动时效处理,可以将游标卡尺的产品不合格率从10% 降到2% ,生产成本仅为0. 26 元/件。从振动时效前后的对比统计结果可以得出,使用振动法可以降低直接经济损失1. 1 元/件,综合可以获得0. 84 元/件的经济效益,由此可见,使用该装置能够取得显著的经济效益。