振动时效工艺能够有效降低应力峰值,均化应力,防止工件变形,哪对半圆薄壁件是否也有效果呢?
薄壁圆筒类工件加工变形比较大,加工精度不容易保证。而对于不封闭半圆弧薄壁圆筒类加工变形比圆筒更为严重,工件加工更是困难。
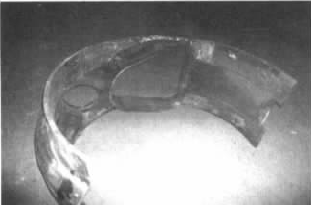
薄壁圆筒类工件加工变形比较大,加工精度不容易保证。而对于不封闭半圆弧薄壁圆筒类加工变形比圆筒更为严重,工件加工更是困难。
大半圆弧形设计结构决定其焊接存在变形,在焊接后还需机械加工外径尺寸。大半圆弧直径工件,壁厚小于20mm而高度近700mm,即加工表面范围大,从而产生加工误差,工件易变形,使局部壁厚不均匀,影响工件本身的强度及后续加工余量问题,进而影响工件的装配使用。
这种结构的工件导致加工难度大,如果车削外圆时是一次车削定尺寸,容易导致加工应力过大,产生工件变形。通过实际生产了解,即使分成几次车削工件,因加工面都在工件的外表面,导致加工量都在工件的外表面一侧,使加工受力不均匀,产生向内弯、扭曲变形。
这种结构的工件导致加工难度大,如果车削外圆时是一次车削定尺寸,容易导致加工应力过大,产生工件变形。通过实际生产了解,即使分成几次车削工件,因加工面都在工件的外表面,导致加工量都在工件的外表面一侧,使加工受力不均匀,产生向内弯、扭曲变形。
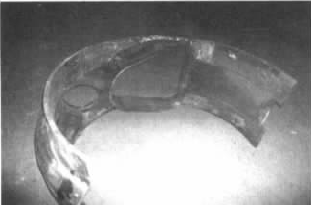
由于该结构件是装配后的运动部件,加工后变形大于8mm,必须用手工砂轮进行打磨外圆尺寸,不但费时而且很难保证尺寸精度,使得该工件严重制约生产并影响了产品使用性能。
为了解决工件加工变形,我们对工件加工工艺进行大量改进。该工件先由两种单件焊接而成,再进行机加工,为防止工件变形,加工前需在工件内圆弧处焊上工艺拉筋,因同时在立式车床加工两个工件,也需在两工件间焊接工艺拉筋。针对车削外圆尺寸,我们分为三次车削,即粗车、半精车、精车,并在半精车削后,工件单边留少量的加工余量,转至振动时效机上进行振动时效。
振动时效技术是采用机械振动方式,消除或均化金属工件内部的残余应力,防止金属工件变形、开裂,稳定工件尺寸精度和位置精度,实现精益化生产的一项实用性技术。振动时效是使工件内部产生动应力,动应力和工件残余应力叠加超过微观屈服极限,产生微小塑性变形,随之引起残余应力降低并重新分布,将粗车和半精车后产生的加工应力进行均化、释放,从而达到稳定工件尺寸精度及位置精度的目的。
工艺过程
经过新的振动时效工艺安排,该工件在精车前内部没有产生半精车加工后的残余应力,所以在精车后工件产生的变形很小,不用矫正就能达到产品图的要求,解决了不封闭半圆弧薄壁筒形工件加工变形问题,为下道装配工序带来保障,现已将新工艺完全固化在工艺文件中。
将工件刚性压在平台上,采用频谱谐波振动时效设备,该设备由计算机自动制定工艺,对激振点、拾振点位置无特殊要求,自动优化选取5个以上振动频率,对工件进行多维消除、均化残余应力。系统对不同的焊接结构件都能准确地选择到共振峰,不会出现旧时效设备找不到共振峰的现象,解决了旧设备必须完全依靠人工操作的问题。
另外,为了与振动时效进行对比,我们对该工件进行过热时效试验,由于工件整体刚性差,热时效试验时工件变形量大,加工余量不够下道工序加工,如果多留加工余量可以保证加工,但再加工后又产生了新的变形,而且热时效试验时间长,使得该件的生产周期影响了工厂生产进度。这表明,热时效试验不适用于不封闭半圆弧薄壁圆筒类工件。
另外,为了与振动时效进行对比,我们对该工件进行过热时效试验,由于工件整体刚性差,热时效试验时工件变形量大,加工余量不够下道工序加工,如果多留加工余量可以保证加工,但再加工后又产生了新的变形,而且热时效试验时间长,使得该件的生产周期影响了工厂生产进度。这表明,热时效试验不适用于不封闭半圆弧薄壁圆筒类工件。

经过新的振动时效工艺安排,该工件在精车前内部没有产生半精车加工后的残余应力,所以在精车后工件产生的变形很小,不用矫正就能达到产品图的要求,解决了不封闭半圆弧薄壁筒形工件加工变形问题,为下道装配工序带来保障,现已将新工艺完全固化在工艺文件中。
结语
通过对工件几处典型加工工艺分析及在实践中的具体应用,特别是合理采用振动时效工艺,解决了不封闭半圆弧薄壁筒形零件加工变形的问题,满足了产品要求,保证了产品质量。
